
The integrated design allows the entire motor, controller, and sensor package to be replaced as a single compact assembly. A rear-facing LED provides diagnostic trouble codes to help quickly diagnose issues. Onboard thermal management protects the CIM and integrated controller from excessive duty cycles at high load. All motor parameters are presented in native engineering units (speed in RPM, voltage in Volts, position in rotations, current in Amps, etc.).įor teams which prefer to avoid CAN communication, Venom may be controlled through a PWM signal. There are no calculations required to convert encoder counts into speed. There are no concerns about mechanical compatibility between third party sensors. The motor controller and speed encoder were designed around the CIM (its rear bearing actually). Venom was designed for convenience and simplicity. WPILib compatible libraries for LabVIEW, C++, and Java are provided. All of these features are accessed via the CAN (Controller Area Network) interface, which is designed for FRC communication. There are also external inputs for limit switches and an analog signal. This includes proportional duty cycle and voltage control, closed-loop current (torque), speed, and servo (position) control, follow-the-leader, and motion profiling controls. So how "smart" is Venom? Speed, current, temperature, and position are all measured onboard, enabling advanced control modes without complicated sensing and wiring schemes. Venom integrates all of these functions into a single, compact package. The traditional CIM is a "dumb" motor, requiring a suite of external controllers and sensors. Therefore, PID tuning is essentially an engineering art that cannot only rely on automated processes but requires the experience of the designer.Venom is a brushed DC motor based on the original 2.5" CIM, which has been used by FIRST Robotics Competition teams for the past 18 years. A variety of techniques such as Gain scheduling are employed to deal with this fact. As the PID is controller, it naturally cannot maintain an equally good behavior for the full flight envelope of the system.
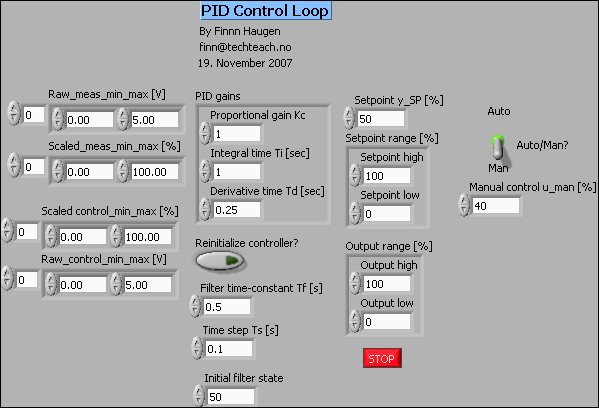
With the exception of hover/or trimmed-flight, an aerial vehicle is a nonlinear system.The integral term needs special caution due to the often critically stable or unstable characteristics expressed by unmanned aicraft.The control margins of the aerial vehicle have limits and therefore the PID controller has to be designed account for these constraints.
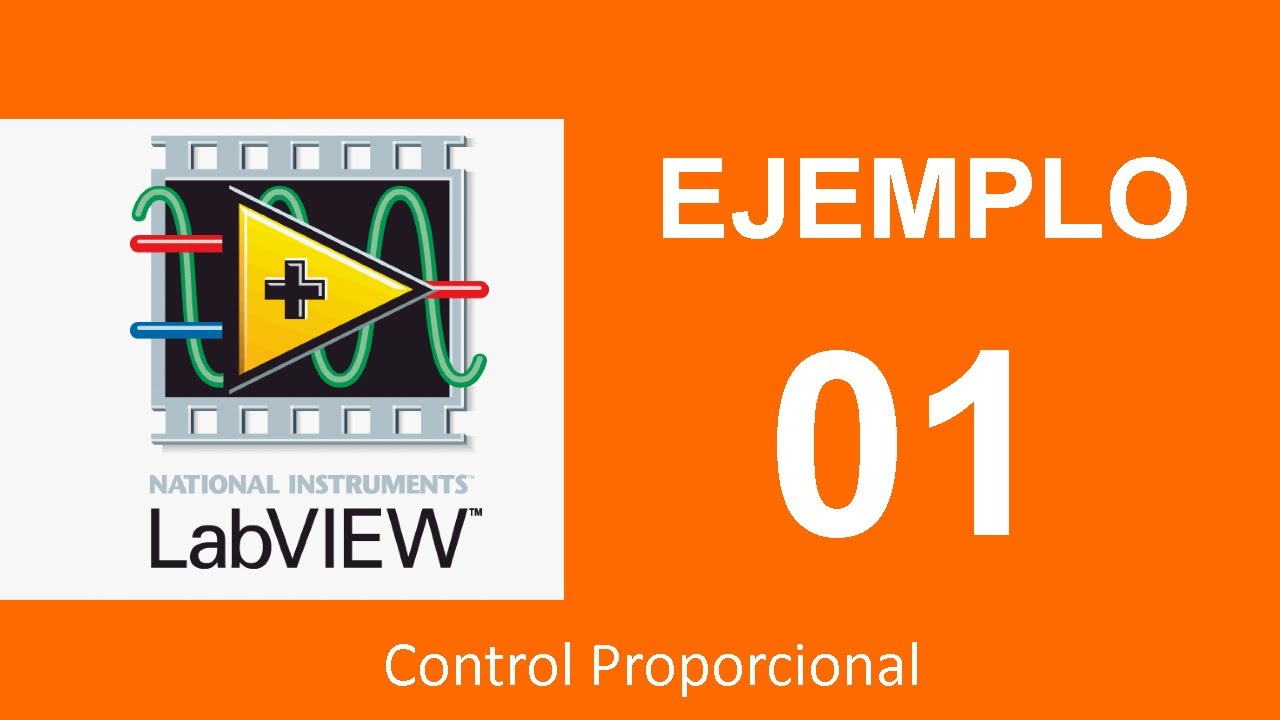
Among others, the following important issues have to be considered when designing flight control functionalities using PID controllers: Real-life implementation of PID controllers is however a much more elaborated process. Nowadays, modern tools exist to optimally tune such control laws. The PID controller is so successful both due its powerful performance and its simplicity.
